一、项目背景
国内某大型钢铁集团公司新建一条热连轧生产线,项目总投资80亿元,设计年产200万t热轧钢卷,计划2009年4月进行热负荷试轧,同年8月正式投产。其中,上海重型机器厂有限公司负责全线机械设备的设计和制造,该厂拥有本条生产线工艺技术的完全自主知识产权,全线采用自动化控制和计算机实时监控,具有结构紧凑、轧制过程连续和生产效率高等优点,达到了国际先进水平。
二、设计流程
设计流程如图1所示。首先建立本条生产线的三维模型,继而进行一些设计检查,其中包括干涉检查和爆炸动画制作等。随后使用COSMOSWorks对关键零部件进行有限元分析,并针对结构缺陷处进行优化设计,然后将三维模型转化二维工程图。为了更好地展示产品,又使用了一款与SolidWorks兼容、基于真实物理环境的渲染软件MaxWell,对生产线的典型设备进行渲染,使用COSMOSMotion对本生产线的运行过程进行动态模拟,并开发出一套可重组模块化轧机CAD系统。
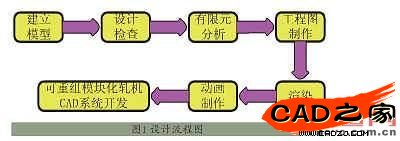
三、三维模型规划及实施
1.设计思想
本文采用“自下而上”结合“自顶向下”的设计思想对本条生产线进行建模和装配。由于本项目结构非常复杂,零部件数量多,难度大,而且是实际生产项目,因此我们在正确建
立零部件的基础上,更多地考虑了产品的优化设计。考虑零件在实际装配体中的位置,建立零部件的设计意图,正确使用几何关系、方程式和尺寸等合理地规划模型,以最简单的建
模方式和最少的特征建立模型。为了方便转化工程图,在设计过程中,严格遵循机械制图的一些规定,合理地规范标注草图尺寸。
2.模型展示
从图2中可以看出,本生产线(如图3)分为粗轧区装配(如图4)和精轧区装配(如图5)。其中,粗轧区装配又由E立辊轧机、R粗轧机以及机前/后辊道组成。精轧区装配由飞剪机、除鳞机、精轧机组以及输出辊道组成。
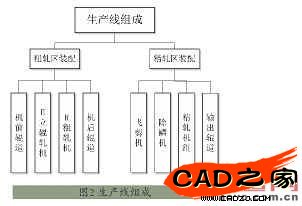
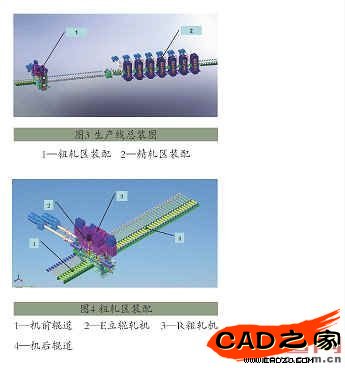
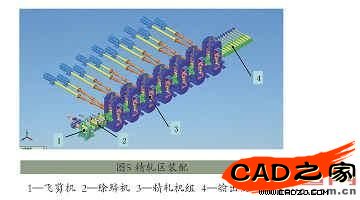
四、设计分析及校验
为保证设计的正确性,运用SolidWorks各种不同的装配关系把各个机械零件装配起来后,对零件的装配体进行静态干涉的检查,可以方便快捷地发现干涉问题。修改零件时,可以点击资源查找器中相对应的命令来完成;也可以在装配环境中进行零件的修改,即点击要修改的零件,进入零件环境来完成修改。后者也显得很方便。
1.干涉检查
对于一个复杂的装配体,利用二维平面图来检查零部件的干涉情况是件很困难的事。使用SolidWorks的干涉检查功能就能很方便地发现干涉问题并进行适当的修改。图6为精轧机干涉检查结果。
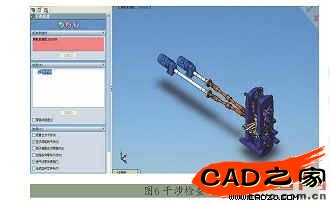
2.爆炸动画
基于指导装配的目的,需要分离装配体中的零部件,以形象地展示它们之间的相互装配关系。装配体的爆炸视图可分离其中的零部件以便查看这个装配体内部结构以及装配过程。
爆炸动画的反过程为装配动画,通过建立爆炸视图,运用与SolidWorks无缝连接的Animator模拟本条生产线的总装配和各设备的独立装配。
五、有限元分析
COSMOSWorks是一款与SolidWorks完全集成的设计分析系统。COSMOSWorks提供了对模型进行应力分析、频率分析、扭曲分析、热分析和优化分析等一整套分析解决方案。本
文使用COSMOSWorks对关键零部件进行了有限元强度分析,对缺陷处进行改进,直到满足设计要求。
1.分析流程
COSMOSWorks分析流程如图7所示。首先建立模型并定义材料性能,划分网格,然后定义空间几何约束、施加力、压强等载荷就可以进行分析。输出分析结果后,对缺陷处进行改进优化后重新进行分析,直到符合要求。
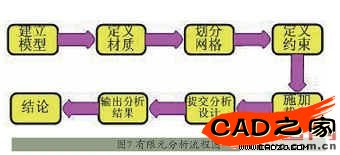
2.实例分析
本文以E立辊轧机牌坊为例,讲解使用COSMOSWorks分析的过程。
(1)定义材质
该零件的材料性能分别为抗拉强度500MPa,屈服强度270MPa,泊松比0.28,弹性模量196GPa,密度7.8x104kg/m3 。在COSMOSWorks中选中材质自定义选项,并输入相关的参数。
(2)划分网格
有限元素分析(FEA)提供了一种可靠的数字方法来分析工程设计。该方法从生成几何模型开始,然后将模型化分为若干简单的方块形状(单元),这些单元连接点称为共同点(节)。有限元分析程序将模型视为由相互连接的离散单元组成的网络。网格化是分析过程中一个至关重要的步骤,E立辊轧机牌坊实体网格划分如图8所示。
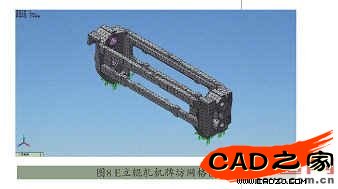
(3)定义约束和施加载荷
载荷和约束在定义模型的服务环境时是不可或缺的。分析结果直接取决于指定的载荷和添加的约束。载荷和约束作为特征被应用到几何实体中,它们与几何体完全关联,并可自动调整以适应几何体的变化。每个约束和载荷条件由COSMOS AnalysisManager树中的一个图标表示。COSMOSWorks提供了与上下文相关选项来定义约束。
由于E立辊轧机牌坊底部装在底座上,我们对牌坊底部的下表面施加固定的约束,即将其所有平移自由度DOF设定为零;牌坊在钢板轧制过程中受到3,000KN的轧制力,并通过侧压螺母传递到牌坊侧压螺母孔上,我们分别在上、下侧压螺母孔表面施加1,500KN的载荷力,如图9所示。
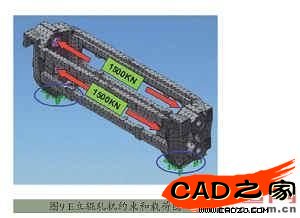
(4)静态应力分析
设置好以上参数后,就可以进行设计分析了,继而输出分析结果,图10a、b和c分别为应力分布图、位移分布图和安全系数分布图。分析结果为,应力最大值53.16MPa,最小值17.78MPa;位移最大值0.69mm,最小值0;安全系数最大值100,最小值8.43。从分析结果中,我们可以得出合格的结论。另外,还可以通过生成可立即发布到Internet的报告,将算例快速、系统地制作成文件。报告组织为说明算例的所有方面。报告中可以自动包括在COSMOS AnalysisManager树中生成图解,也可以在报告中插入图像、动画(AVI视频)和VRML文件,自动生成易于打印的报告。
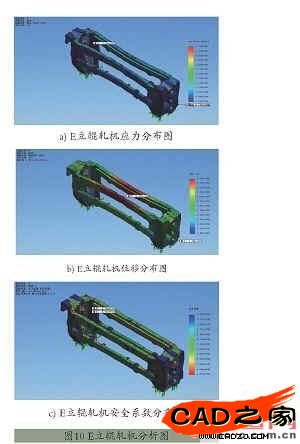
六、工程图生成
三维设计结束后,将3D实体零件和装配体创建成2D工程图,用于加工制造。零件、装配体和工程图是互相链接的文件;对零件或装配体所作的任何更改都会导致工程图的相应变更。图11为本生产线中某一零件工程图。
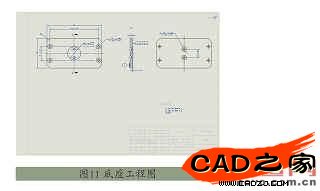
七、高级渲染
为了高效地展示设计思想,减少样机和摄影成本,缩短产品开发周期,快速地将产品投放入市场,渲染技术便应运而生。它作为表现产品的一种高效手段,近年来随着计算机硬
件和图形学的发展,在业内得到了日趋广泛的应用。在上述使用SolidWorks完成三维造型的基础上,我们采用渲染,制作出具有真实质感和良好视觉效果的图片,高效展示我们的产品和设计思想。它是一款基于真实光线追踪技术的渲染引擎,采用光线追踪算法,完全重现光线的行为,以此产生专业照片级的效果图。
在SolidWorks界面下,我们可以直接使用对应插件渲染模型和场景,其主要功能及操作如下。
1)打开模型,使用Solidworks摄像机调整观察角度,并创建场景;
2)在Solidworks中对各零部件直接应用相对应的Maxwell系统材质;
3)设置照明光源和相关渲染参数,并进行渲染;
4)渲染完成后使用灯光模拟系统调节场景照明。
由于本生产线零件数目多,外形结构复杂,我们采用了分布式渲染(把单帧图像的渲染分布到多台计算机上渲染的一种网络渲染技术)以保证渲染的顺利完成,并提高了渲染质量,得到部分渲染效果图如图12所示。
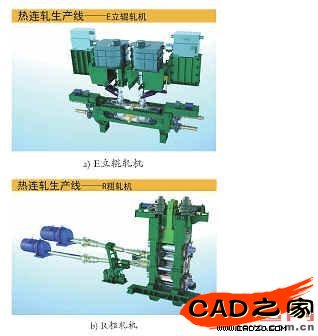
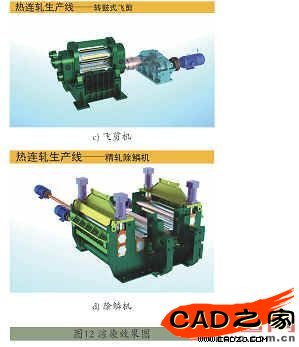
八、动画仿真
COSMOSMotion是一款与SolidWorks无缝集成的全功能运动仿真软件。COSMOSMotion可用于建立运动机构模型,进行机构的干涉检查,跟踪零件的运动轨迹,分析机构中零件的速度、加速度、作用力、反作用力和力矩等,并用动画、图形和表格等多种形式输出结果,其分析结果可指导修改零件的结构或者调整零件的材料。
设计的更改可以反映到装配模型中,再重新进行分析,一旦确定优化的设计方案,设计更改就可以直接反映到装配模型中。
轧钢过程具有驱动多、动作复杂和控制难度大等特点。我们利用COSMOSMotion实现了轧钢过程的全程模拟,即毛坯板从铸造炉出来经过本生产线的宽度控制、粗轧厚度轧制、
切头、切尾及精轧等最终形成成品板材的全过程。其中难点为钢板由厚变薄、由短变长以及钢板切头与切尾等过程。
COSMOSMotion动画仿真流程如图13所示,建立好零部件后,在COSMOSMotion中,对静止零部件和运动零部件进行映射,然后定义约束。由于COSMOSMotion与SolidWorks无缝集成,普通约束通过SolidWorks中的装配关系都能转化为COSMOSMotion中的运动副。定义完约束后,需要添加附在运动副上控制运动的运动参数,即运动驱动。当所有参数都设置好就可以进行运动模拟,继而可以进行动态干涉检查和输出各种分析曲线和视频。
图14为动画截图,其中图14a为轧制前的毛坯板,图14b为粗轧以后的中间板坯。与毛坯板相比,中间板坯厚度、长度都有明显变化。
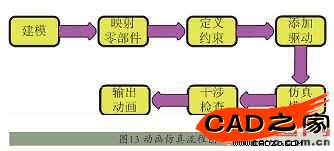
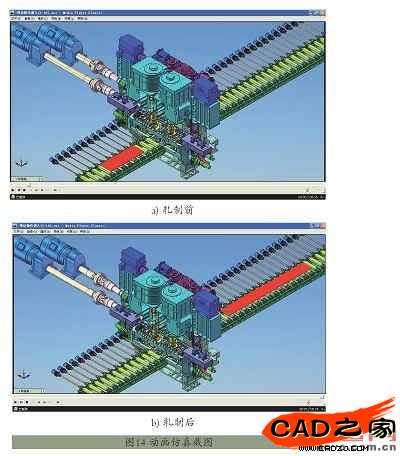
九、可重组模块化轧机CAD系统开发
由于轧钢机结构复杂,设计制造过程中采用“单件小批”的模式,而这在很大程度上制约了轧机的设计周期。为了解决这个问题,本文引入可重组模块化思想,将轧机划分为几个独立的模块,并建立各个模块内部以及模块之间的参数化约束,最后通过一个自动建模装配函数来实现不同模块的装配。从而设计出了一套“基于SolidWorks可重组模块化轧机CAD系统”,如图15所示。利用此系统,用户只需要输入轧制线标高、开口度、工作辊直径、工作辊长度、支撑辊直径及支撑辊长度等参数,即可得到所需参数的模块化轧机。
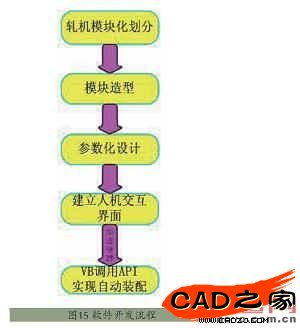
1.开发流程
本系统的总体设计目标为:只要用户给出基本的构型参数,系统就能够自动建模装配
产生用户所需要的一台模块化轧机。
结合软件的设计方法,设计主要由五部分组成。首先将轧机进行模块化划分。按照可重组模块化思想,将轧机划分为机架装配、工作辊装配等十几个模块。各个模块具有独立的功能,同一类模块的外部接口需类似。第二,进行模块构造,这部分在建模、装配阶段已经完成。第三,进行参数化设计,建立模块内部以及模块之间的一些参数联系。第四,建立
人机交互界面,获得用户所需要的参数。第五,调用Solidworks API,编译一个装配函数。这样,用户所需要的参数传递给装配函数,就可以实现自动建模装配。
2.软件介绍
“基于SolidWorks可重组模块化轧机CAD系统”具有如下特点:界面美观,可以更换不同的皮肤界面;使用简单,只需输入一些基本参数,系统将自动建模装配一套指定参数的模块化轧机;实用性强;软件界面如图16所示。
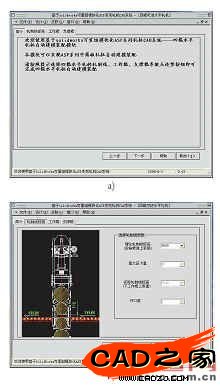
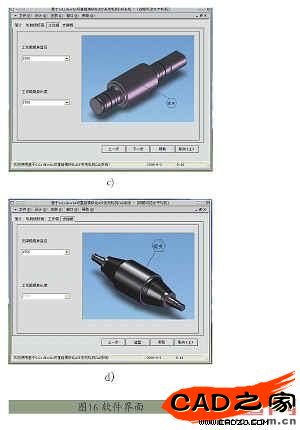
3.自动装配技术的实现
使用VB调用SolidWorks API函数,通过API函数在客户端应用程序中创建SolidWorks对象,并依次创建PartDoc、AssemblyDoc等子对象,来完成模块化轧机的自动建模装配。装配
函数如下:Sub Assembly(ByVal WRD As Integer, ByVal WRL As Integer, ByVal BURD As Integer, ByVal BURL As Integer,ByVal KKD As Integer, ByVal ZBG As Integer, ByVal GBG As
Integer)SetswApp= CreateObject("Sld-Works.application")
' 创建或获sldworks对象
Set swModel = swap.ActiveDoc
'激活文件
……
swModel.EditRebuild3
swModel.ViewZoomtofit2
swModel.SaveAs2 App.Path + “temp” + “可重组模块化ASP系列轧机.sldasm”, 0, False, False '保存文件End Sub
4.软件运行实例
打开软件,进入设计界面,所有参数如图16所示,最终得到一个如图17所示的模块化轧机。
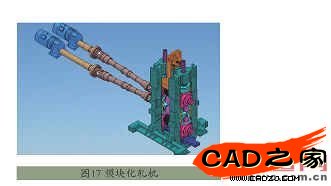
十、总结
本项目的主要成果有:
1)建立了一条热连轧生产线的三维零件库,为今后的产品设计和改进提供了再使用的宝贵资源;
2)对本条生产线重要零部件进行了强度校核,验证其强度符合设计要求;
3)对本条生产线的轧钢过程进行了动画仿真,发现设计缺陷并进行改进,缩短了设计时间,极大地提高了设计效率和设计质量;
4)使用渲染软件进行渲染,提高了产品的附加值;
5)使用VB调用SolidWorks API函数,实现了不同参数的ASP系列轧机的统一模块化重组,为轧机的三维参数化设计提供了一种快速有效的途径。
本文对热连轧生产线做了大量的研究工作,已经具备一定的实用功能,但还有许多不完善的地方,需要以后进一步的开发和设计。比如,没有涉及换辊等设备,CAD系统目前只完成了粗轧机的可重组开发等。这些工作将在后续的工作中做进一步的研究。
在以后的工作中,有以下课题需要深入研究和应用。
1)轧钢设备三维设计规范及有限元分析规范的制定。规范的制定,可以帮助企业三维数字化平台的快速推广,便于设计交流和扩充。
2)轧钢设备研发知识库的建立。依托SolidWorks Enterprise PDM系统,将企业现有的数据资源进行归纳、总结、规范并管理,实现设计知识的继承及重载。
3)专用CAD系统的深入开发;
将现有的系统开发从VB平台迁移到先进的net平台,便于扩充和协同开发;
在参数化设计过程中加入优化功能;
实现符合标准的工程图自动生成;
实现COSMOSWorks自动分析系统。
因此,以SolidWorks为平台的CAD/CAE/PDM解决方案将在轧钢设备的设计过程中发生重要的作用。
相关文章
- 2021-09-08BIM技术丛书Revit软件应用系列Autodesk Revit族详解 [
- 2021-09-08全国专业技术人员计算机应用能力考试用书 AutoCAD2004
- 2021-09-08EXCEL在工作中的应用 制表、数据处理及宏应用PDF下载
- 2021-08-30从零开始AutoCAD 2014中文版机械制图基础培训教程 [李
- 2021-08-30从零开始AutoCAD 2014中文版建筑制图基础培训教程 [朱
- 2021-08-30电气CAD实例教程AutoCAD 2010中文版 [左昉 等编著] 20
- 2021-08-30电影风暴2:Maya影像实拍与三维合成攻略PDF下载
- 2021-08-30高等院校艺术设计案例教程中文版AutoCAD 建筑设计案例
- 2021-08-29环境艺术制图AutoCAD [徐幼光 编著] 2013年PDF下载
- 2021-08-29机械AutoCAD 项目教程 第3版 [缪希伟 主编] 2012年PDF