箱体类零件定位销孔加工方法和加工机床
时间:2011-06-02 08:33:07 来源:未知
1 概述
气缸体、气缸盖等箱体类零件定位销孔的加工一直是关键工序,箱体类零件的显著特点是工艺复杂,要求加工内容多,零件需经多台机床、多道工序以至于反复加工才能完成。由于定位销孔是加工机床主要的定位基准,箱体类零件的加工精度在很大程度上取决于其定位销孔的精度,特别是定位销孔的位置精度,它还影响其它工序的加工精度和整机的性能(如汽车发动机)。因此国内外各厂家都在努力地提高定位销孔的加工精度,寻求最佳的加工方法。国外定位销孔的加工位置精度由过去的±0.03mm(也有的为±0.05mm)已提高到现在的±0.02~±0.025mm,个别的为±0.015mm。国内目前定位销孔的位置精度已达到±0.025~±0.03mm,比国外略低一些。随着汽车工业的发展,我国的汽车工业也将进入世界行列,这些数值必须达到国外先进水平。因此如何提高定位销孔的加工精度其意义重大。
2 工艺方法
目前,国内箱体类零件两定位销孔的加工方式均采用模板导向套的钻、铰工艺或钻、扩、铰工艺。刀具在导向套引导下工作,刀具与导向套相对运动,存在着间隙,一般能达到的位置精度为±0.05mm。新的导向套保证精度略高一些,但随着导套的不断磨损精度逐渐降低。通常两定位销孔的位置精度只能稳定保证在±0.05~±0.08mm之间。不少发动机生产厂家为了提高这种工艺方法加工的位置精度,采用了多种措施,大致有以下几种手段:
- 提高钻模板导向孔精度,坐标精度为±0.005。
- 加长导套的引导长度,L/d>3~5,导套的配合精度为H6/g5,形状误差不大于0.005。
- 尽量减少导套至加工孔间距离。
- 为保证模板定位精度,采用过定位方法(3~6个圆柱销)来固定模板。
采用这些方法后可相对提高定位销孔的位置精度,但要保证或提高钻模板的导向精度就需要定期对夹具进行拆卸,重新修正。模板底孔对钻套配合间隙的控制,一是通过分别确定各导套适应本工序加工精度所要求的间隙,二是根据实际生产情况和铰刀引导部位的实际尺寸进行选配。夹具部分经常性维修造成了大量拆卸、装配、调整工作,给维护和管理带来了困难。
国外定位销孔的加工精度为±0.02~±0.025mm,一般采用数控机床或加工中心进行加工。有的厂家也采用带硬质合金导向套的加工方法,这种导向套的导向孔是与刀具配磨的,导向套靠近工件表面,以提高孔加工的位置精度。但这种方式刀具磨损很快。总之,这些加工方式虽能保证定位销孔加工的位置精度,但大大增加了设备投资。
3 定位销孔加工机床
我们设计的缸盖定位销孔加工机床,采用刚性钻、铰新工艺方法。设计前做了大量试验工作,包括刀具切削速度对钻孔偏移量的影响、刀具进给速度对钻孔偏移量的影响、刀具悬伸长度l对钻孔偏移量影响。实验证明,仅刀具悬伸长度l对钻孔偏移量有影响,其它因素均影响不大(在常规下可以忽略不计)。
刚性钻孔试验简图如图1。
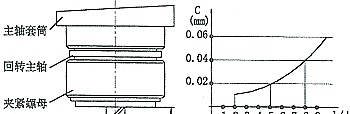
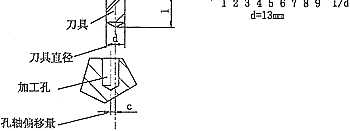
图1 刚性钻孔试验图
注:1.l为刀具悬伸长度 2.本实验在坐标镗上进行试验 3.铰孔可进一步纠正钻孔时的偏移量
工件预先有底孔时,采用精密镗削(或刚性镗削)能够加工出位置精度很高的孔,如:在坐标镗上镗孔。
工件无底孔而且要求钻孔的位置精度很高时,通常在钻孔前打中心孔,以保证孔位置精度,但不及前者加工精度高。为了保证机床具有高的孔加工精度和适宜批量生产,采取如下措施。
- 采用短钻头、短铰刀,提高刀具系统的刚度。
- 采用高精度、高刚度的单轴镗削头组成的四个镗削头(其中两个用于钻孔,两个用于铰孔),实现轴间距可调(轴间距可调至±0.005以内),保证孔的位置有很高的精度,而且可实现多品种加工。
#p#分页标题#e#
- 采用高刚性的双工位移动工作台进行钻孔与铰孔。
- 加工中不采用导向套具有以下优点:
- 采用短钻头、短铰刀,使加工部位接近主轴端部,加工孔位不易偏移,易保证孔位置精度。
- 不存在导向磨损,易于长期保持稳定的加工精度,并使维修费用大大降低。
- 刀具切削速度可提高1~2倍。当采用高速钢钻头进行刚性钻孔时,切削速度可达到40m/min以上;采用硬质合金钻头进行刚性钻孔时,切削速度可达到60m/min以上。机床生产率大大提高。
- 采用结构简单、敞开性好、便于操作观察、排屑流畅、维修方便的夹具。
由于采用了以上措施,该机床加工出的定位销孔位置精度很高,达到世界先进水平。