1 引言
目前三维CAD/CAPP系统在采用直接集成方法时,大多通过开发专门的特征识别模块,以提取CAD模型中的几何信息和特征信息,以供CAPP系统使用。这种集成方法对特征识别技术的成熟度和可靠度要求较高,不仅技术难度大,而且~旦特征识别的结果出现偏差,将直接导致CAPP源头数据的错误。此外。通过特征识别方法实现集成,无法体现出三维CAPP在工艺流程编制、工序简图绘制方面的优势。以回转体类零件为例,研究特征设计方法与三维CADICAPP集成系统,采用直接集成方法,避开了特征识别模块的开发,基于SolidWorks软件提供的特征设计工具和配置管理工具,有效地实现了CAD/CAPP系统的集成,大大提高了回转体类零件工艺设计的效率。
2 CAD/CAPP直接集成存在的问题
2.1 特征识别技术成为集成的关键与瓶颈
在CAD/CAPP直接集成方法中,特征识别技术成为集成成功与否的关键。特征识别主要是对几何模型进行解释。以鉴别出特定应用的特征,它是将几何模型与一些预先定义好的“样板特征”进行比较,从而确定相匹配的特征实体。然而,特征识别方法本身也存在一些缺陷。如对于曲面特征和相交特征,识别难度大、容易出错;对于复杂零件的特征识别,计算量大,识别效率不理想;对于复杂特征的识别,容易产生多重解释,需要人为判断与修正。基于这些原因,致使特征识别技术成为CAD/CAPP直接集成方法的瓶颈。
2.2 特征模型包含的数据无法满足工艺要求
通过特征识别技术得到的特征模型,一般只含有零件的几何信息,没有包含零件的工艺信息,如尺寸公差、材质、表面粗糙度、加工精度等级等。现在人们已经普遍认识到这种状况不合理,应该改变。虽然特征识别技术现在已经能够从CAD模型中提取出部分工艺信息,但仍然无法满足CAPP系统的要求。例如特征模型经过特征识别后得到的信息只能辅助CAPP系统中工艺装备的设计。基于特征信息进行工艺决策自动生成工艺流程,虽然具有一定的工艺智能性,但技术难度大,工艺流程的合理性欠佳,目前也尚无成熟的系统出现。另外,对特征模型进行特征识别,无法模拟CAPP系统中零件从毛坯到成品的变化过程。
2.3 工序模型和工序简图的绘制工作量大,效率低
工序简图是机械加工的图形表达形式,它和工艺设计卡片一起作为车间生产的指导性文件。用手工方法绘制工序简图效率低、工作量大、标准化程度差,而且不能与工序模型动态关联,一旦三维工序模型发生更改,工序简图需要重新绘制。在三维CAPP系统中,只有工序简图自动从工序模型派生,才能从根本上减少绘制和修改简图的工作量,那么工序模型的设计自然而然成为了提高工序简图绘制效率的关键。特征识别无法模拟零件的工艺成型过程,因而不能有效提高工序模型的设计效率,进而对整个CAPP系统的运行效率产生影响。
3 面向工艺的特征设计技术
3.1 特征的分类与定义
基于特征设计的CAD造型方法,是由设计人员按照特征建立产品模型,在设计、制造、分析等各个阶段都采用特征进行信息的存储和处理。在零件设计时,采用形状特征来构成零件的结构。回转体类零件的形状特征可以分为主要特征、辅助特征和基准特征,结合回转体零件的加工方法,主要特征和辅助特征又分为外特征和内特征。主要特征是构成零件基体的主要元素;辅助特征依附于主特征,对主特征的局部结构进行描述;基准特征是特征之间进行定位和参考的依据,包括基准点、基准线、基准面、基准坐标系等。在进行特征拼合时,特征之间的位置和尺寸约束直接决定了特征建模的成功与否。为此,在定义特征时,为每—个特征都添加了参考引用和尺寸。参考引用是将特征添加到特征模型中时与其他特征进行拼合的依据,所有的特征都至少包含一个方位基准面参考。尺寸是对特征进行几何修改的依据。特征定义的关系图,如图l所示。
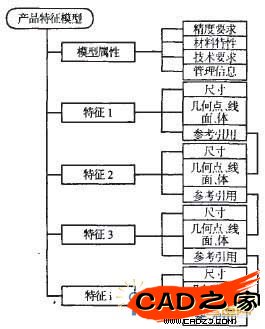
图1 特征定义关系图
3.2 面向工艺过程的特征设计方法
面向工艺过程的特征设计方法,通过特征建模的形式来模拟零件从毛坯到成品的变化过程。这种设计方法要求产品设计人员熟悉产品的制造工艺。在进行特征建模之前,首先根据产品的工艺过程将零件进行分解,获得每道工序所对应的工序模型;然后根据工序模型所包含的特征,从已经建立好的特征库中寻找相应的特征本体;再将特征在设计窗口中实例化后,通过特征拼合的方式进行特征建模,最终得到完整的产品模型。回转体零件的特征建模过程,如图2所示。
图2 面向工艺过程的特征建模
3.3 特征模型与CAPP中工序模型的关联
在三维CAPP系统中,工序简图是从工序模氆派生的。如何准确快速地设计每道工序对应的工序模型,成为提高工艺设计效率的主要因素之一。在CAD/CAPP集成系统中,如何将特征模型与CAPP中的工序模型进行关联,自然成为了研究的热点。系统利用面向工艺过程的特征设计方法,结合SolidWorks平台提供的配置功能,有效地实现了特征模型与工序模型的关联,极大地提高了CAPP系统中工序简图的绘制效率。在工艺设计过程中,每道工序对应—个工序模型,同时该工序模型对应产品特征模型的一种配置。配置是在产品特征模型的基础上,完全通过特征的压缩与释放得到的。特征模型与工序模型之间的映射关系,如图3所示。
图3 特征模型与工序模型的映射关联
利用提出的面向工艺过程的特征设计方法进行产品的特征建模,可以非常轻松地获得特征模型的不同配置,从而得到每道工序的工序模型。同时,在工艺设计过程中,工艺尺寸的修改可以直接驱动工序模型的尺寸,工序简图则会自动刷新。另外,与该工艺尺寸相关的其他工序中的工艺尺寸和工序模型也会相应自动刷新,有效地实现了工序模型与工序简图之间的横向、纵向关联,极大地提高了工艺设计的效率。
3.4 特征信息与工艺信息的关联
特征信息与工艺信息的相互关联,如图4所示。
图4 特征信息与工艺信息的关联
4 应用实例
以工程油缸中的导向套零件为例,在SolidWorks平台上进行特征建模时,首先应建立好完备的产品特征库。导向套零件包含圆柱基体特征,端面台阶特征,内部槽特征,孔特征,圆角特征,倒角特征等。在特征定义时,为每个特征指定参考和尺寸(图略)。对端面台阶特征的定义及其与圆柱基体特征的拼合。根据零件的结构特征和工艺过程,将导向套分解为下料、车左端外圆及端面、车右端外圆及端面、车端面沟槽等设计特征;再利用SolidWorks软件提供的库特征功能,按照面向工艺过程的特征设计方法进行特征建模;最后得到产品的特征模型。
在进行工艺设汁时,首先从特征属性中提取工艺流程信息;然后通过特征的压缩与释方如进行工序模型的侧十。每道工序对应特征模型的一种配置,导向套零件的配置信息(图略)。每道工序的工序简图由工序模型自动派生,工序尺寸可以从工序模型属性中提取.也可以通过人机交互的方式从模型结构上拾取。最后将工艺装备等相关的工艺信息全部存棍倒工艺数据库及工序模型的配置属性中,以供二雏工艺卡片设计时直接直接调用,最终生成的工艺卡片信息。
5 结语
研究了面向工艺过程的特征设计方法与CAD/CAPP集成技术方案;分析了需要解决的若干关键技术,并以SolidWorks为平台,通过详细的实例,阐述了特征设计方法在特征建模过程中的应用以及集成过程中信息的关联,对CAD/CAPP系统集成技术的研究具有一定的参考意义。在后续的研究工作中,建立设计特征与加工特征之间的映射关系,同时将工艺决策的信息融入到集成过程中,可以有效地实现CAD/CAPP集成系统的智能化。
相关文章
- 2021-09-08BIM技术丛书Revit软件应用系列Autodesk Revit族详解 [
- 2021-09-08全国专业技术人员计算机应用能力考试用书 AutoCAD2004
- 2021-09-08EXCEL在工作中的应用 制表、数据处理及宏应用PDF下载
- 2021-08-30从零开始AutoCAD 2014中文版机械制图基础培训教程 [李
- 2021-08-30从零开始AutoCAD 2014中文版建筑制图基础培训教程 [朱
- 2021-08-30电气CAD实例教程AutoCAD 2010中文版 [左昉 等编著] 20
- 2021-08-30电影风暴2:Maya影像实拍与三维合成攻略PDF下载
- 2021-08-30高等院校艺术设计案例教程中文版AutoCAD 建筑设计案例
- 2021-08-29环境艺术制图AutoCAD [徐幼光 编著] 2013年PDF下载
- 2021-08-29机械AutoCAD 项目教程 第3版 [缪希伟 主编] 2012年PDF