笔者所有的3-D编程经验均来自于Mastercam软件,所用的许多术语都是Mastercam中使用的,但是大多数CAM系统都有一些类似的特征。虽然这些特征的名称并不相同,但在您的系统中仍具有同样的功能。
模具曲面
为了获得一个良好的曲面刀具路径,您必须以一个良好的曲面为起始。如果您用来生成曲面所应用的软件与您用来生成刀具路径的软件不同,您最好花些时间先检查所生成的曲面。
您需要定义“正曲面法线”的方向。曲面法线是在曲面上通过一个切点与切面相垂直的一条矢量。它可以附属在每一个单独表面,而不是一个具体的工件外形。在下图中,绿色箭头指的是矢量通过与曲面的交点垂直于曲面,而且它们指向正曲面法线。
每一个曲面有两个法线,方向相反。一个方向为正(向前,向外);另一个方向为负(向后,向里)。正法线曲面通常是您所加工的曲面。当一个曲面被生成时,默认法线的方向是基于定义曲面的方向而决定。在您加工模具时会出现一个问题,正法线中一些方向向里,一些方向向外。必须改变这些法线的方向,使所有的法线指向同一方向。在下面的图例中,左面曲面中正法线指向外测,右面曲面中正法线指向内侧。
确认曲面法线方向是非常重要的,因为它会影响由曲面生成曲线时的偏置方向,平面投影至曲面的法线方向,及在两个面之间生成另一个连接曲面的方向。
同时,也请检查曲面生成公差或最大表面公差,在曲面上生成曲线时的最大距离。如果公差被定义过大,将不能够加工出理想的表面。
技巧:我通常设置最大的表面分离公差为0.00005" (0.0013mm)。
选择正确的曲面刀具路径
所有的CAM系统提供了多种曲面刀具路径。在选择曲面粗加工路径时,根据工件的成品形状和您所预留的加工裕量来决定所采取的刀具路径。如果您想在工件的内部切削(也就是切一个槽)曲面槽刀具路径通常是一个明智的选择。如果您想加工一个实体或者是切削一个工件的外形,最好选择曲面轮廓表面加工路径。大多数曲面粗加工以等深的Z轴方向向下步进,同时,为精加工的曲面留下特定的裕量。在粗加工中,Z轴的阶深会影响精加工裕量。阶深越大,精加工的裕量也就越大;反之,阶深越小,精加工的裕量也就越小。
显然在Z轴方向小步进将会增加加工时间,所以在编程时主要考虑三个主要因素:材料类型、精加工刀具尺寸和要求的表面光洁度。如果您加工比较软的材料,例如铝或软钢,粗加工所留下的大块材料不会对精加工有太大的影响。如果您加工比较硬或难切削的材料时,当刀具开始接触到粗加工所留下来的均匀的加工面时,您的刀具可能会变形,从而产生不均匀的光洁度。
有两种常规的方法可解决这个问题,在粗加工中应用较小的Z轴步进量或者是增加一个半精加工刀具路径可以比精加工刀具路径粗糙。同时,使用另一把刀可以使和精加工一样的刀具尺寸的刀,但是必须是另外的刀具。如此一来就可以避免在精加工和半精加工时使用同一把刀具,导致磨损加快。
技巧:通常地,半精加工路径将留有0.005"到0.015" (0.127到0.381 mm)做为精加工裕量。
在粗加工时,使用较小的Z轴步进量及仿形
因为它被设计用切削片与工件作大面积的接触,不同于一般的铣刀盘,所以它是一种很壮的刀具,可以以较高的进给切削从而缩短加工时间。在作等深的Z轴步进时,不同于90度的端面铣刀,圆形的刀片同时可以让您在粗铣非垂直表面时,留下较小的裕量。绝大多数的硬质合金刀具制造商都生产这类的铣刀盘,您可以选择不同的铣刀盘制经济不同的切削片直径来满足不同的加工需求。
图:以任意的Z轴切削深度使用仿形铣刀具时,将留有教少的切削余量。
曲面精加工路径
选择表面精加工路径不是一件易事。为了获得高质量的曲面精加工路径,必须了解一些基本的概念。在99%的加工中,精加工刀具路径是由球形铣刀生成的。这种形状允许它可以在所有的表面上移动,在球面上的任何点都可以切削。例如,将一颗钢珠放在碗中,您可以在碗中将钢珠滚至任何位置,而该钢珠与碗都是点接触,这个点取决于钢珠在碗中的位置,而接触点我们称为切点。
图:在图中, 碗状物的半径是0.250" (6.35 mm), 球形刀具的半径是0.125" (3.175 mm).
下一个概念是径向步进.。径向步进是两个连续平行切削的中心距离。当径向步进增加的时候,尖端高度将会较高。尖端高度是决定加工曲面光洁度的首要因素。尖端高度为0.00003" 到0.00005"(0.00076到0.00127 mm)时,您可以得到不错的表面光洁度。因为尖端高度是由径向步进(rso)和刀具直径而定,所以我们可以得出以下是计算平面尖端高度的公式:
当选择精加工刀具路径的时候,首先要考虑所需要的表面光洁度。如果您加工一个模具,曲面光洁度必须格外光滑,与切削一个具有较大光洁度公差的曲面相比,您将做出不同的选择。
第一种类型的精加工刀具路径为平行路径。刀具进给以直线平行来通过整个加工曲面。这些直线型切削不一定会平行于机床轴。它可以在任何角度加工,但是所有通过曲面的加工路径都要平行的。在大多数情况下,这样的刀具路径可以切出最好的表面光洁度。
平行的刀具路径可以以两种方式完成——往复式及单向式。单向式刀具路径在沿某轴方向走刀之前,以快速移动的方式将Z轴升高,回到起始点旁的一个步进距离,Z 轴降低,在平行于前一方向走刀,依此循环。值得一提的是,所有的切削进给方向是平行的。往复式刀具路径是在刀具路径平行往复变换,变换距离为一个步进。
技巧:根据我的经验,平行铣削将会产生较好的表面光洁度,但是花费时间较长,因为它在每一次走刀的行程都必须反复定位。Z形铣削在一个方向是顺铣,在另一个方向是逆铣。这通常会产生不均匀的表面,在质地较硬或难切的材料时,刀具磨损会较快。
环形刀具路径是另外一种常用路径。在整个曲面,环形铣精加工路径能够在加工曲面上保持一致的高度。刀具一直与曲面相接触,使收缩运动减少到最小。这种路径的工作方式非常好,它可以从外部开始以环形向中心运动,或者是从中心开始向外部以环形运动。缺点是不论它向外部运动或者是向中心运动,当在曲面上改变切削方向时,会在加工过的表面留有“可见刀痕”。一般在半精加工过程中这种加工路径非常有效,因为它可以去除在粗加工时留下的阶状材料。当不需要特别好的表面光洁度曲面时可以用到它。
环形刀具路径: 刀具路径在曲面上改变方向.
环形铣刀具路径
平行铣削刀具路径: 在曲面上的每一次铣削都与其他的路径相互平行.
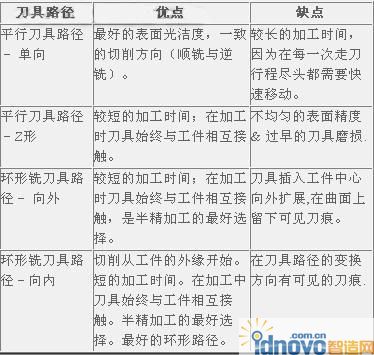
切削公差
在所有的曲面刀具路径中,刀具路径的循环精度是由“切削公差”来控制的。它有时候以线性公差为参考。线性公差决定了弧性误差(刀具路径与实际曲线,曲面或实体面的距离)的曲面精度。切削公差将刀具路径线性化时,决定刀具路径如何更接近实际曲线,曲面或实体面的距离。
由于刀具路径是线性的(所有的刀具路径移动G01,线性进给),刀具不可能总是与曲面保持绝对的接触。因此,刀具路径与实际面有可定义的公差。当刀具路径与实际面接近刀切削公差值时(刀具偏离实际面的时候)一个运动指令块会把刀具路径带回至曲面接触。反之,而将刀具路径带离曲面,当刀具接触到曲面的时候,又有一个指令块避免过切削。
因为此种线性路径,被加工的曲面是由一系列的面组成,我们称为多面体。您可以想象一个钻石,乍眼一看,它是一个圆的锥体,但实际上是由许多平面组成。如果在一个加工曲面刀具路径切削公差过大,曲面将是由较大的平面组成。同时,因为刀具路径偏离实际面,您将在加工过的表面上看到许多划痕。这些划痕不是实际面的过切——它们仅仅是执行线性进给时留德未切材料。这是因为刀具在以连续的步进沿着真曲面加工时,不完全是以相同的量,相同的方向偏离实际面。要解决这个问题,定义较小的切削公差将会减少划痕和缩小构成曲面的平面。
技巧:为了获得高光洁度的曲面,我建议设置切削公差为0.00002"(0.000508 mm)。
在上面的照片中,使用相同的刀具,在相同的主轴速度,进给率和步进条件下切削相同的形状. 除了切削公差外, 所有的因素都相同. 照片1的切削公差为0.00033" (0.008 mm). 照片2的切削公差为0.00002" (0.0005 mm). 表面精度的差别确非常明显。
过滤刀具路径
在生成复杂的3维表面G代码文件时,过滤刀具路径是缩小该文件的最好方法。过滤刀具路径的时候CAM系统在规定的公差内置换刀具路径,它会用一个线性指令去取代一条直线运动。这与上面讨论的设置切削公差为最小值意图相反,但是如果您设置切削公差与过滤公差为相同值,将减少很少代码量。现在我们可以在不降低精度的情况下,设置弧过滤器以减少G 代码量。
应用刀具过滤器,只要规定弧最小和最大的误差,就可以替代多个线性刀具路径,可以在XY,XZ,或YZ平面选择创建弧线,但是刀具移动必须与加工轴相平行,获得弧线输出。设置弧线过滤器参数可以使由平面组成的多面体曲面更加平滑,因为刀具路径过滤器可以用一条弧形指令取代多个线性指令,从而减少G代码使用量。
高速加工
哈斯控制系统中的高速加工选项,通过分析程式中从一个行到另一个行的矢量方向变化,或者角度的改变,来实现高速加工,从而缩短加工周期。当在矢量方向的改变较小时,例如使用代码生成较小的切削公差值时,控制器可以以较高的进给速度运动;这比矢量方向改变的较大时,所产生的进给速度要大。矢量方向改变得越大,编程的路径在控制器上输出的运动会越慢。正是因为这个原因,您不希望把刀具推入一个内槽的尖角。在一行的程式指令中,为了加工一个尖角而瞬间改变方向时,机床的运动会接近完全停止。刀具在尖角中接近停顿的瞬间,会使刀具压力及刀具变形降低,这使得刀具会在加工表面的相交处产生刮痕。您应该在加工编程中,让内弧半径大于刀具半径,或者选择的小于内弧半径的刀具。这样可以使刀具行进方向作大改变时,由多个小方向改变的程式完成,从而让机床运行更平顺及快速,同时加工面也更为光滑。
在左图中显示在尖角区的切削加工.在一个块代码中矢量方向改变120度,将导致加工突然慢下来.如果刀具在这个方向上缓慢改变,将会明显的减少循环时间.
哈斯高速加工选项可以每秒1000块的速度进行——也就是每千分之一秒(1毫秒)执行一行程式。为了获得平滑,流线般的运动,您程序中任何指令的执行速度不能少于1毫秒。例如,如果您的进给速度是每分钟150英寸,也就是每秒2.5英寸。如果用每秒2.5英寸除以1000,您将发现,在每分钟150英寸的进给速度下,您的行程是每毫秒0.0025"。 您可以用下面的公式计算使用线性指令时三维移动距离 (D) (d =轴移动距离):
G-代码确认
左图中,客户的工件上留有切面。右图中使用Metacut软件分析的客户G代码程序,生成的结果提示客户问题在于程序,而不是刀具。
Metacut 软件功能有图形编辑,确认,档案和元素分析,背景测绘及图形文件比较。它使您能够点击在程式中任何代码块并立即分析它。该软件可以显示每个程式中的起始点,中点,终点的X,Y和Z轴坐标。它也可以计算在所有轴联动时,每个轴的2维距离或者是3维距离。您可以在www.metacut.com网上下载此软件,有30天的免费试用期。这个软件可以帮助您检查程序是否有问题,例如撞机。当然,它更大的作用在于铣加工程序中,确定工件表面光洁度。
在右图实际加工中显示的线与应用Metacut软件中显示的线是相同的(左图).
总结
1.检查您要加工的曲面,确定能够加工。
2.检查仿形铣刀盘粗加工路径是否为加工工件的正确方法。
3.用球形端铣刀精加工,设置步进量,产生可以接受的尖端高度。
4.设置切削公差符合所需要的表面光洁度。
5.在可能的情况下过滤成弧线。
6.在切削工件前确认G代码。
7.如果结果不符合您的要求,再次确认G代码,放大检查看起来有问题的区域。这将帮助您决定问题是由程式造成的或是其它因素。
8.如果有任何疑问,请联系您所使用CAM系统的技术支持,刀具厂商或者是机床厂商。
在加工3-D曲面之前,一个最好的建议是应用一套G-代码确认软件来检查错误。几乎每套CAM系统都有刀具路径确认功能。问题是您在用CAM系统生成程式,而数控机床读取并执行的是G代码。程式生成过程中会产生很多情况,尤其是如果您在上面描述的状态下使用刀具路径过滤器。在哈斯的每一位应用工程师的电脑里都配有 Metacut Utilities软件。 Metacut是一套不十分昂贵的软件,它可以读取G代码并生成精确的工件模型,使得应用工程师都在切削之前就知道工件的样子。
我们经常听见客户抱怨在加工的时候工件上有划痕,但是在用Metacut软件做G代码分析的时候,可以在模拟的图形上看见痕迹。铣刀可以减少加工时间。仿形铣刀是一种装有圆形切削片的铣刀盘,但是它并不像与球头铣刀般有着正圆的外形。这类圆形的切削片因为所切出的切削并不等原,所以进给速度可以较快,取决于切削深度,进给切入角可以从0度到90度,一般说来,仿型刀在切削时是十分平顺的。下图:大型圆刀片端铣刀,也是所谓的“仿形铣刀具”或“钮式刀具”。
相关文章
- 2021-09-08BIM技术丛书Revit软件应用系列Autodesk Revit族详解 [
- 2021-09-08全国专业技术人员计算机应用能力考试用书 AutoCAD2004
- 2021-09-08EXCEL在工作中的应用 制表、数据处理及宏应用PDF下载
- 2021-08-30从零开始AutoCAD 2014中文版机械制图基础培训教程 [李
- 2021-08-30从零开始AutoCAD 2014中文版建筑制图基础培训教程 [朱
- 2021-08-30电气CAD实例教程AutoCAD 2010中文版 [左昉 等编著] 20
- 2021-08-30电影风暴2:Maya影像实拍与三维合成攻略PDF下载
- 2021-08-30高等院校艺术设计案例教程中文版AutoCAD 建筑设计案例
- 2021-08-29环境艺术制图AutoCAD [徐幼光 编著] 2013年PDF下载
- 2021-08-29机械AutoCAD 项目教程 第3版 [缪希伟 主编] 2012年PDF